Valve Train Tribology Research Essay
Executive Summary
The valve train tribology exercise was conducted to explore the parameters influencing the selection of lubricants for valve train components. The analysis entailed the examination of variation of minimum lubricant film thickness with oil grade, camshaft speed, oil temperature and change of maximum Hertz contact stress with camshaft speed. film thickness data generated several insights, including the shape and type of plots that were drawn according to the operating conditions described below, and an explanation for the ensuing behaviors.
Aims and Objectives
The main goal of the experiment was to examine factors that affected the lubricant of valve train parts. Additional issues that were also tested during the investigation included that definition of tribology, the essential components of engine tribology, features and functions of a lubricant in a typical automotive engine, as well as lubricant additives.
Literature Review
During the production of performance engines, engineers and customers often target to build a performance engine that surpasses its theoretical expectations both in terms of revolutions per minute and output. Since customers do not design the engine, they are limited to selecting better parts and in some cases, doing the best they can with what the market offers (Omasta et al., 2018). Before engine tribology assessment and power and the effects of fluids can be looked into, it is worth noting that tribology examines ass aspects of interacting surfaces in constant movement. The examination entails friction that causes failure and generates heat and wear. However, lubrication can be used to overcome the adverse effects of continuous motion. The lubricants replace solid to solid contact.
In principle, lubrication is a crucial part of an engine. Lubricants can be in the form of mineral oil or synthetic. Mineral oil lubricants are commonly used in a variety of applications. It includes a substantial amount of saturated hydrocarbon molecules in ring structures that are in equilibrium. However, it should be noted that the particles provide little protection to engine parts or surfaces if fluid film lubrication is not active. Contrastingly, synthetic lubricants are available in the form of silicones, acid esters, phosphate esters, polyglycols, fluorocarbons, and synthetic hydrocarbons, to mention a few (Jahanmir, 2016). Organic acid esters offer a wide temperature range, but they are expensive with reduced viscosity range. Polyglycols offer a wide viscosity and temperature range, but they are similarly expensive.
Matthews, & Sadeghi (2016) state that a lubricant can also be used to conduct heat away from an engine, remove wear debris and prevent the production of deposits on bearing surfaces. Therefore, it is suggested that a lubricant should be non-aggressive and chemically stable, should be able to stick to surface when a system is powered off and must environmentally friendly reduce pollution. The selection a lubricant should also consider factors such as density, viscosity, heat capacity, chemical composition and pour point, which is the lowest temperature at which grease can flow or pour. Viscosity can further be measured using rational or cone-on-plate viscometers that use varying techniques.
According to Sadeghi, & Sui (2016), there is a substantial amount of information that can be leveraged to examine camshaft analysis. The analysis of theoretical data entails the discussion of what a valve should do when as it transitions from one cycle to another such as opening and closing. In some instances, the system can be supplemented with a rocker arm or a follower ratio that superimposes the open valve plot along the curve lobe tube lift curve. The development can further be supported by an illustrating a motion of the valve via a familiar opening cycle. In theory, the movement of the valve could match the data generated from the curve, but in practical applications, the actual valve characterization can vary from what is predicted.
Furthermore, it should be noted that the data generated from examining valves does not reveal what other factors influence the valve, and what the equipment does in real-life. To begin with, in real-life applications, a factor referred to as ‘compliance’ should be examined (Paranjpe, & Gecim, 2012). The element discusses movement, compression, and flexing of the valve train parts during the action. The influence of some of the factors is insignificant, but when combined, they can illustrate why valve open curves shift from predictions.
For instance, there is the issue of the cam bearing clearance. In particular, the bearings need oil clearance to keep the bearing functional in an extended period and ensure that the cam moves in the defined limit of clearance, although in some scenarios, the motion does not align to factors that should theoretically support valve action. Rather than accurately following the projected cam curve or lobe, the valve loses lift, as well as a section of a shift in valve timing points.
Omasta, Adam, Sperka, Krupka, and Hartl (2018) discuss that camshaft deflection has a crucial influence on the stability of valve trains. For example, in addition to the movement of the bearing, the camshaft also bends when subject to the valve spring loads, which leads to a loss in lift due to the extra lift on the camshaft. Furthermore, the authors state that hydraulic lifters have and influence on valve train stability since there is always some form of internal hydraulic leakage when compressive loads are applied to the system. Effectively, the addition leads to more loss of lift, which may require changes in the designed valve curve.
Moreover, further valve train components can be examined in terms of pushrods. Specifically, in pushrods enginers, the parts compress particularly as valve string pressure is supplemented to the production components. In addition, loss in lift and a shift in the curve can be observed as is the case with factors mentioned above. In fact, the pushrods can permanently compress or flex before making a rebound that can induce additional shock in the entire valvetrain setup. In some cases, the rocker arms and rocker followers can affect the operation of valve train components. In particular, rockers and their supporting parts such as mounts can flex under excessive valve spring loads. Afterward, the system can experience increased spring pressure and heightened rocker ratios, which can then lead to flexing, particularly in combination with production tools.
According to Mufti and Priest (2013), designers can choose the best components in the valve train from camshaft bearings to stabilize the system when the engine is at high speeds to avoid failure. To this end, camshaft bearing analysis plays a pivotal role as it can be leveraged to limit motion off the center of rotation, as well ensure that plain bearings do not wear and tear, to keep the recommended oil clearance at constant high engine speeds. Moreover, if options were explored, it would be advised to select camshafts with additional and larger bearing journals so that tall cam lobes can be achieved, which also feature a larger core diameter. However, the analysis does not entail the design of an engine because it is limited to examining available materials. In addition, stiffness can be maintained by ensuring that cam lobes are not subject to grinding. Lastly, valve spring pressures should be sufficient to manage action but not substantially high to impart unnecessary loads on the camshaft.
Discussion
According to Table 1 above, the camshaft speed was maintained for Case 1 to Case 4 before it was doubled in Case 5. It increased further to 1200 and 2500 rpm for case 6 and 7 respectively. Afterward, the speed was dropped back to 400 rpm for the rest of the cases. Secondly, it was noted that oil temperature remained the same at 40 degrees Celsius for case 1 to case 7. The temperature value was 0 degrees Celsius for case 8 but increased to 60 and 80°C for case 9 and 10 respectively. The highest oil viscosity was recorded in Case 8 at 3.8311 Pa.s, whereas the minimum value was recorded in case 10 at 0.0313Pa.s. The majority of the cases used oil grade SAE 50, except for case 1, 2, and 4 that used SAE 30, SAE 40, and SAE 60 respectively.
In Figure 1 above, it was possible to measure lubricant film thickness with an acceptable range of precision. The thickness at the inlet and outlet cam was not the same because the curves were not a mirror reflection of each other. It was challenging to determine the extent of the scatter in the plots was based on the variations of the film and measurement inaccuracies, although some of the erratic curves were linked to signal noise and interference from the operations of the piston land (Taylor, 2017). The plot, however, was not sufficient enough to investigate the properties of the bearing. Therefore, it was necessary to subject geometric tolerance to truncation during design.
In Figure 2, the variation of the minimum lubricant film to the camshaft speed was a replica of the oil grade at the outlet and inlet. Valvetrain frictional loss in terms of camshaft speed was, therefore, linked to the interactions between the device and the tappet. According to Figure 3, it was apparent that thermal effects contributed to the operations of the system, including sliding conditions. In the chart, it could be inferred that a surface entering a contact area was subject to low temperature, which also matched ambient temperature (Priest & Taylor, 2013). Further actions such as heating were associated with viscous work and compression, while the heat produced in the engine relied on the load, the lubricant film, and sliding speeds that were a function of viscosity influenced by temperature and pressure (Arshad et al.,2017). Finally, Figure 4 demonstrates that the engine was probably in an over speed state. Specifically, it the maximum value of contact stress was unmatched, and the peak time was observed at its earliest, effectively affecting the stability of the system (Taylor, 2013). It also heightened the cam-tappet wear, which could possibly cut engine life.
Conclusions
In sum, the exercise was successful in describing the variation of minimum lubricant film thickness with oil grade, camshaft speed, oil temperature, and change of maximum Hertz contact stress with camshaft speed. The following conclusions were made grounded upon operations of the engine and the thickness of the lubricant film. In high-sliding activities, the dimple scenario affected the lubricant film thickness substantially. Notably, ambient temperature was central to improving operations, although minimum film thickness could be explored. Secondly, no direct connections were made between the gradient of the plots and factors such as temperature. The exercise also revealed that the variation of maximum Hertz contact stress with camshaft speed was insignificant, although asymmetry in the thickness of the lubricant film was in line with the wedge effects.
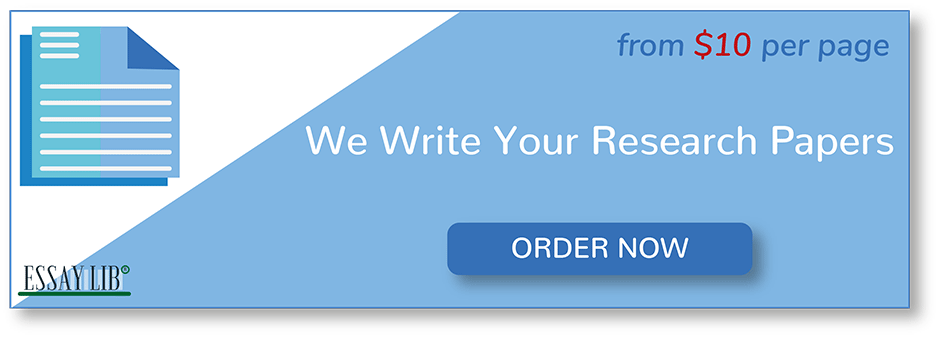
References
Arshad, W., Hanif, M. A., Bhutta, M. U., Mufti, R. A., Shah, S. R., Abdullah, M. U., & Najeeb, M. H. (2017). Technique developed to study camshaft and tappet wear on real production engine. Industrial Lubrication and Tribology, 69(2), 174-181.
Jahanmir, S. (2016). Examination of wear mechanisms in automotive camshafts. Wear, 108(3), 235-254.
Matthews, J. A., & Sadeghi, F. (2016). Kinematics and lubrication of camshaft roller follower mechanisms. Tribology transactions, 39(2), 425-433.
Mufti, R. A., & Priest, M. (2013). Effect of engine operating conditions and lubricant rheology on the distribution of losses in an internal combustion engine. Journal of tribology, 131(4), 041101.
Omasta, M., Adam, J., Sperka, P., Krupka, I., & Hartl, M. (2018). On the Temperature and Lubricant Film Thickness Distribution in EHL Contacts with Arbitrary Entrainment. Lubricants, 6(4), 101.
Paranjpe, R. S., & Gecim, B. A. (2012). Comparative friction assessment of different valve-train types using the FLARE (friction and lubrication analysis) code (No. 920491). SAE Technical Paper.
Priest, M., & Taylor, C. M. (2013). Automobile engine tribology—approaching the surface. Wear, 241(2), 193-203.
Sadeghi, F., & Sui, P. C. (2015). Compressible elastohydrodynamic lubrication of rough surfaces. Journal of tribology, 111(1), 56-62.
Taylor, C. M. (2017). Automobile engine tribology—design considerations for efficiency and durability. Wear, 221(1), 1-8.
Taylor, C. M. (2013). Valve train-cam and follower: background and lubrication analysis. In Tribology Series (Vol. 26, pp. 159-181). Elsevier.