Wind Turbine Blade Erosion
Introduction
During their operation, the winds turbines are exposed to a wide variety of both the atmospheric and environmental conditions; Due to this, the blades show a varying degree of leading edge erosion. Leading edge erosion is a substantial risk to wind turbine performance and blade maintenance (Sareen, pg,1531). The attempts to investigate the effects of the leading edge erosion on the blades of the wind turbines is carried out using the Computational fluid dynamics (CFD) method.
Over the past few years, wind power generation has developed significantly due to its clean and renewable characteristics. The scope and the size of the modern wind turbine have emerged as a result of the need to capture the wind energy and the development of the technology. A single turbine can produce energy in the range of 8-10W with their diameter of being around 160m.
During the operations of the wind turbines blade, they are eroded due to rain and hail, and even due to insects. Erosion will mostly occur in the outer blade region due to the difference in the relative inflow velocity which is higher at the exterior than in the inner parts of the blades. The measurements of the effects of erosion on the aerodynamic are rare, and corrosion is known to lead to higher drag and lower lift mostly at angles of attacks near the stall.
The mechanical integrity of a turbine is affected by various environmental factors such as raindrops, sand, hailstones and any other harsh airborne particles. The manufacturing and the operations of the wind turbines are affected by a various factor, and the leading edge erosion is the primary challenge that they face (Chinmay, pg, 525). The decay is due to the formation of the small pits near the leading edge. With time they combine slowly and leads to the creation of the gouges. Failure to repair in time will result in the continuous growth of the gouges, which leads to the production of the delamination.
The Leading edge erosion may have severe effects such as loss of power due to the induction of flow separation and transition to turbulence. Understanding the influence of leading edge erosion on a wind turbine is essential to mitigate the adverse effects and can be used in the wind turbines maintenance, and wind farm operators’ management.
Leading edge erosion has been documented to adversely affect the aerodynamic characteristics of an airfoil which results in the loss of lift and increase in drag. This, in turn, affects the energy harvesting characteristic of the wind turbine. Cavity erosion on the leading edge can give rise to the occurrence of the leading separation bubble and flow separation at the trailing edge. This plays a significant role in the lift decrease and drag increase of the airfoil.
The paper analysis on the blades of a wind turbine due to “Leading Edge Erosion and how it affects the performance with the use of the numerical. The work shall look at how the leading edge erosions affect the working of the turbine and provide a simulation by the use of the CFD on the same with consideration of various factors. After the verification of the numerical methods, the data that was collected involves the aerodynamic polar of clean, eroded and coated airfoils and they were generated employing the CFD.
The Process of Erosion
The erosion starts with the formation of small pits near the leading edge. This increases the density as time passes by and combine to form a gouge. The gouge if not maintained and left to the forces of nature they grow in size, density and mix to form cause delamination near the leading edge. To prevent erosion, it is possible to use special prominent edge protections. Protection that is used can reduce the effect of corrosion. Example of security is the one that is used in the blades of the helicopter which are eroded by rain and sand. Then material of helicopter blades and the coating that is used should be noted is different from the user in the wind turbines as it is the speed of the rotors and the flow behavior.
There has been researching by the various researcher on the wind turbines, and different conclusion have been achieved. As according to Fernandez, after computing the airfoil polar employing Computational Fluid Dynamics (CFD) and used the extreme in the BEM computations to estimate the power output of a 5MW turbine (Gaudern, pg, 524). By the use of such an approach, he was able to determine the factors that may lead to the Lead edge erosion and how they affect the performance of the turbines.
The Methods
The sections describe the methods that were used in the collection of the data. The aerodynamic coefficient is computed employing CFD and validated for the primary approaches.
The primary challenge in the turbo machinery applications is the introduction of a rotating body to apply forces on the fluid. (E.g. Compression or Expansion). Rotation is supposed to be introduced in the constitutive equations of motion which can be done in two approaches; the moving reference frame (MRF) and the sliding Mesh (SLM). The MRF consists of the rewriting NS equation in a rotating frame, while SLM introduces rotation by the use of a rotational component of velocity to all nodes of the domain (physical grid rotation). The SLM approach is more realistic than the MRF (Sagol,pg,514).It has a more CPU demanding because the computational model needs to be re-meshed at every time advancement during the simulation procedure.
The rotation of grid intrinsically depends on the time-evaluation of simulation. The approach is not recommended as for steady-state simulations because the solution that is obtained is not time dependent. A steady calculation performed with MRF approach according to the evidence in most of the turbo machinery problems does not compute a time perfect solution.
The coefficient of the airfoils in this work was computed employing CFD. The process involved the solving of the RANS (Reynolds-averaged Navier- Stokes) equations. The roughness effect on the airfoil has experimented into a two- dimensional simulation. The calculation suggested that the CFD is necessary with the use of rough wall functions. It should be known that the roughness phenomenon cannot be reduced to only change the transition point location.
To be able to close the RANS equation, an equation for intermittency was added in order to consider transition from laminar to turbulent flow. The use of two dimensional meshes (hexahedral) with a 512 cells on the airfoil and a 256 cells in the airfoil’s normal direction which then lead to approximately 130,000 cells. A dimensionless wall distance of y+ < 1 was used and the radius of the domain was 80.c, where c is the chord length of the airfoil.
The close-up mesh and a complete domain view of CFD two dimensional. To be able to simulate the rough walls, there was the use of the wall functions, where there was a modification of the coefficient of the law of wall. This leads to a higher dimensionless wall distance of y+ = 30 leading to the reduction of the number of cells by 192 cells.
Strong erosions lead to delamination and a change in the leading edge shape. The heavy abrasions cannot be modelled with the wall functions, and thus there is a need to simulate a different edge shape. There can be the use of fully- turbulent flow model which lacks transition, but have a resolved boundary layer.
The performance of Mesh studies is carried out for all the levels of roughness. Each review is carried out in three different meshes with the same domain size and similar y+ values. I am moving from one mesh to a more beautiful mesh led to the doubling of the number of cells in the radial direction and along the airfoil. Where the rough wall functions are used, a higher dimensionless wall distance and accordingly fewer cells in the radial direction were used. The relative difference is calculated based on the lift and drag coefficient resulting from the fine meshes (Zhang, pg, 103). There is a recording of improvement when a medium-mesh is used as compared to the coarse mesh.
The simulation of the airfoil with different shape leads to a higher resolution of the airfoil shape, which means there are more cells along the airfoil, which in turns lead to a different representation of the Kink at the leading edge. This is an indication that with different meshes, slightly different geometries are simulated, which indicates the disadvantage of such a mesh study and explain the higher deviation of the drag coefficient for the eroded airfoil. The medium meshes are considered to deliver sufficiently converged results at a reasonable computing time.
The clean and rough simulation follows the experimental trend, and some deviations are observed to stall. This occurs when the CFD overpredicts the lift and the coefficient. It is a common problem when it comes to turbulence models, the results from the two- steady dimensional simulations, but three- dimensional measurements of unsteady flow. By the concept of the rough wall functions, it is impossible for the inclusion of complete erosion details as the approximations in the modelling approach contains some limitation like the airfoil shape not being changed and the simulated roughness being evenly distributed which isn’t the case in reality.
When we compare the clean and rough simulation, a deformed shape that was caused by the steady erosion indicated a stronger decrease in the lift and an increase in the drag near the stall. The most potent erosion type does not lead to deformation as it happens on the real wind turbines. With the various method of modelling clean, rough and eroded airfoils, a broad range of surfaces can be simulated.
The computation of coefficient by the use of the CDF are loaded in turbine load calculation to test for the effects of erosions and leading edge protection by the use of the NREL 5MW turbine. There is the computation of the power, thrust force and root bending moments are computed within the FAST by the method of the AeroDyn Theory Manual equation. The vertical wind shear is calculated using power- law (Sareen, pg,1542).The pitch angles are kept constant between different cases to have a more precise performance comparison of the different airfoils. Air viscosity is calculated as 1.464 *10-5 m2, and the air density is taken as1.225kg/m3
The validation of the CFD methods is carried out. Afterwards, there was the simulation of the airfoils with the different leading edges shapes but with the same computational set-up. There is a change in the distance of the wall while the dimensionless wall distance remained the same. The simulation of the airfoils was done with clean and rough configurations. A changed leading edge shape simulated that of the strongly eroded airfoil. The results were compared to a coated leading edge. The different chord of distribution together with rational speed along the radius of the wind turbine blade led to the use of two Reynolds’s number (7.5 *106 11.5*106). There was the limiting of the computational effort, through the failure to generate the airfoil polar for a complete range of 360 degrees.
As discussed earlier strong erosion ca delaminate and deform the leading edge of a rotor blade. When the simulation results of such a shape are compared with the original airfoil under the clean and rough conditions, when the comparison is made against a clean airfoil, the irregular wall function configuration leads to a reduction in the lift near the stall and a general increase in drag. When the eroded is used, the elevator is further decreased. Meanwhile, the pull in the booth is increased, and the minimum drag is smaller than at rough conditions. Rough and eroded airfoils have worse aerodynamic performance than the clean airfoil.
To prevent erosion or to repair eroded wind turbine blades, mounted on a special landing edge protection can be done. It can be also be applied to the leaves after the initial installation. The coating applies to turbines without even removing the blades. However,this reduces the cost compared to other techniques since the shut-down time is shorter, and the general maintenance effort is smaller when compared.The deviation is highly dependent on topography, blade geometry, tower height and weather. On the issue of erosion, rain and hail could erode leading edge erosion on a wind tunnel model from observation of in-service blades 9Sagol,pg,5140. To stimulate roughness, the airfoil is tested through five general configurations: clean, two-dimensional step, distributed toughness, combined roughness and erosion. Field measurement of the insect roughness from the current study is incredibly sparse, potentially due to cleaning from the rainfall.
The primary challenge in the turbomachinery applications is the introduction of a rotating body to apply forces on the fluid. (E.g. Compression or Expansion). Rotation is supposed to be introduced in the constitutive equations of motion which can be done in two approaches; the moving reference frame (MRF) and the sliding Mesh (SLM). The MRF consists of the rewriting NS equation in a rotating frame, while SLM introduces rotation by the use of a rotational component of velocity to all nodes of the domain (physical grid rotation). The SLM approach is more realistic than the MRF. It has a more CPU demanding because the computational model needs to be re-meshed at every time advancement during the simulation procedure.
Geometry Shape
Erosion on a wind turbine depends on the airfoil geometry. The main factors that affect the airfoil when it comes to the geometry are the suction peak on the upper side and the curvature of the leading edge. The two factors drive the maximum erosion rate. The analysis included testing of various airfoils by the use of the CDF. A different family of the airfoil were used which include the NREL and the DU airfoil families. The eroded blade is thus clearly led to lower thrust near the rated wind speed, whereas the sharp edge only slightly decreased the push. The difference between the coated and the stainless blades was negligibly small.
Comparing the lift and drag coefficient for the airfoils with the same size of the defect, therefore it can be perceived that the effect of the deficiency grows with the increase in the angle of attack. The geometric shape determines the angle at which the defects occur. The leading edge defect has a significant influence on the aerodynamic coefficients of the airfoil, which can remain constant when the defect length reaches a critical value. The error grows with the increase of angles of attack.
The wind turbine blade designers have aimed at producing roughness insensitive airfoil shapes. The insensitivity is assessed by comparison of the performance of the data from the numerical simulation which includes the natural transition, to the data whose transition point is fixed at the leading edge. Airfoils are sensitive to contamination, and the sensitivity tends to increase with the increase of corruption.
An investigation on the shape deviations indicated that manufacturing defects, erosions, or sand build could have a tremendous effect on the maximum lift performance. The difference is highly dependent on topography, blade geometry, tower height and weather. On the issue of erosion, rain and hail could erode leading edge erosion on a wind tunnel model from observation of in-service blades(Sareen, pg,1537).. To stimulate roughness, the airfoil is tested through five general configurations: clean, two-dimensional step, distributed toughness, combined roughness and erosion. Field measurement of the insect roughness from the current study is incredibly sparse, potentially due to cleaning from the rainfall. In the areas that are not manifested with insects, their insect roughness is estimated through the calculation of in viscid flow field around an airfoil after which there is a determination of path particles by the use of the Langtry Menter framework.
The Langtry framework introduces two non- physical flow parameters that work together with the one another to determine the criteria the local flow has to meet to induce transition, and once triggered, ramp up to a fully turbulent state. The first depends on the intermittency. It differs from the physically defined parameter of the same name in that it acts as a scaling parameter instead of representing the exact value of the turbulent state. In the laminar boundary layer, the intermittency variable shuts off the production of turbulent kinetic energy (K), and once local criteria are met, it is progressively used to activate the dynamic energy output.
The second variable is defined as the transition onset momentum thickness Reynolds number. It uses the transport equation to be able to take the local pressure gradient and take the empirical correlation as by the freestream turbulence intensity and introduce the local effects. The quantity Reynolds number is compared with the other local flow quantities and used to trigger intermittency production and subsequent ramping of turbulent kinetic energy, attempting to mimic the physical transition process.
Some researchers have suggested the modification of the transition onset criteria from roughness height and displacement thickness. This has also led to the introduction of field quantity that is governed by an additional transport equation that is used to define a region of roughness influence. The scalar field then modifies the transition onset criteria (Zhang,pg,514). The transport equation, in this case, does not involve an explicit production as the distribution of the additional scalar that is introduced in this project is determined with a boundary condition at rocky walls where the user inputs a representative equivalent sand-grain roughness variable.
In this study, the primary flow variables are calculated with the sixth order differencing where the approximate factorised form of the Bean- Warming pentadiagonal scheme is put into practice. It is then followed by the discretisation of the spatial fluxes of the roughness model by the use of the Harten Lax van Leer (HLLC) upwind scheme as the extension of the existing Langtry Menter model with the linear matrix solved using similar successive symmetric over-relaxation (SSOR) algorithm.
To be able to access the impact of the degradation on the performance of a wind turbine rotor as a whole, there was the application of the roughness model to the geometry shape of the NREL 5- MW. The analysis is done on both the clean and rough configurations. Afterwards, tables are created for both the unmodified and the dirty conditions. In addition to this, there was the computation of the various wind distribution change in the annual energy production (AEP) to improve the understanding of the difference in performance due to the roughness. The result indicated that there was less effect from paint- chip roughness. As the distributed roughness height and density increase, the maximum lift coefficient, and the lift to drag ratio decreases.
The lift-drag ratio is an essential parameter for the airfoil design. Increase in the angle of attack the value increases. The lift and drag coefficients change rapidly when the erosion depth is smaller while they reach almost plateau when the erosion depth is more significant. Compared to a stainless blade, an eroded blade led to a decrease in the aerodynamic power for all the wind velocities. When a rough and clean surface is compared the result are in a similar trend. The coated blade with leading edge protection reduces the power only slightly when compared to the clean knife.
The eroded blade is thus clearly led to lower thrust near the rated wind speed, whereas the sharp knife only slightly decreased the push. The difference between the coated and the stainless blades was negligibly small. Thus Leading edge erosion will not lead to an increase in thrust, and the airfoil section with leading edge protection led to a similar push as a stainless blade.
The aerodynamic performance of the airfoil section can be studied by the distribution of the pressure over the airfoil pressure and suction surface. It can also be attributed to the highly skewed cells present in the grids due to the sharp trailing edge of the various airfoil sections used in the real-time wind tunnel testing of the three airfoil sections as compared to the CAD model used in the computational study.
The First and the Second run
The runner efficiency is calculated based on the available and extracted the power of the runner. The obtained energy is derived from the torque generated from the running blades and the rotating speed of the turbine. The available power was collected from the discharge and the clear head within the runner. The efficiency curves have similar trends in all the profiles as they it was found that the lowest efficiencies were part of the load condition and whenever the flow is minimal (Gaudern,pg,524).The rise of efficiency, in this case, is associated with the reduction of the leakage flow in the asymmetric profile. The rotation of grid intrinsically depends on the time-evaluation of simulation. The approach is not recommended as for steady-state simulations because the solution that is obtained is not time dependent.
The change in the fraction of the total efficiency can also be due to the difference in the outlet angle. The increase in the stagnation angle at the inlet of the runner increases the swirl components. The leakage flow, which is considered as the flow passed inside the clearance gap from high pressure to low pressure, can be interpreted from the velocity vectors plotted inside the hole. The real swirling strength is produced by the positive value of the discriminant of the velocity gradient, with the tensor for the complex eigenvalues. This is an indication of the existence of swirling motion around the centre and the difference between the first run and the second run.
Conclusion
The scope and the size of the modern wind turbine have developed as a result of the need to capture the wind energy and the development of the technology.
The measurements of the effects of erosion on the aerodynamic are rare; corrosion is known to lead to higher drag and lower lift mostly at angles of attacks near the stall.
The manufacturing and the operations of the wind turbines are affected by the various factor, and the leading edge erosion is the primary challenge that they face. The decay is due to the formation of the small pits near the leading edge
Leading edge erosion has been documented to adversely affect the aerodynamic characteristics of an airfoil which results in the loss of lift and increase in drag.
The paper analysis on the blades of a wind turbine due to “Leading Edge Erosion and how it affects the performance with the use of the numerical. The work shall look at how the leading edge erosions affect the working of the turbine and provide a simulation by the use of the CFD on the same with consideration of various factors.
Strong erosions lead to delamination and a change in the leading edge shape. The heavy abrasions cannot be modelled with the wall functions, and thus there is a need to simulate a different edge shape. There can be the use of fully- turbulent flow model which lacks transition, but have a resolved boundary layer.
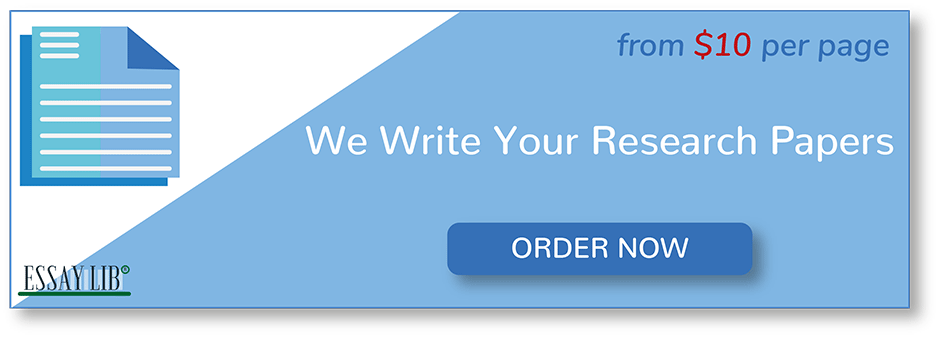
Work cited
Sareen, Agrim, Chinmay A. Sapre, and Michael S. Selig. “Effects of leading edge erosion on wind turbine blade performance.” Wind Energy 17.10 (2014): 1531-1542.
Sareen, Agrim, Chinmay A. Sapre, and Michael S. Selig. “Effects of leading-edge protection tape on wind turbine blade performance.” Wind Engineering 36.5 (2012): 525-534.
Gaudern, N. “A practical study of the aerodynamic impact of wind turbine blade leading edge erosion.” Journal of Physics: Conference Series. Vol. 524. No. 1. IOP Publishing, 2014.
Sagol, Ece, Marcelo Reggio, and Adrian Ilinca. “Issues concerning roughness on wind turbine blades.” Renewable and Sustainable Energy Reviews 23 (2013): 514-525.
Zhang, Shizhong, et al. “Erosion of wind turbine blade coatings–design and analysis of jet-based laboratory equipment for performance evaluation.” Progress in Organic Coatings 78 (2015): 103-115.